
- Homepage
- Customer Stories
- Composites Aragon, il tail light della Bugatti Chiron
Customer story
Composites Aragon, il tail light della Bugatti Chiron
Come si ottiene la cornice del fanale posteriorie della Bugatti Chiron partendo da 197 kg di alluminio e arrivando al pezzo completamente finito e lucidato di soli 1,5 kg di peso.
Quando si pensa ai luoghi in cui vengono prodotti i componenti per le automobili più veloci al mondo non viene subito in mente la Spagna. Invece proprio nel cuore della regione di Aragón, a Zaragoza, un’azienda con un DNA votato alla flessibilità, al dinamismo e al raggiungimento di obiettivi sfidanti sta fabbricando componenti unici nel loro genere.
Nata alla fine del 2009, l'azienda si è specializzata nella produzione di componenti in materiale composito e il suo punto di forza è dato dalla gestione dell'intera catena del valore: dall'ideazione alla progettazione, fino alla messa a punto del prodotto finito. Mettendo assieme le competenze di management e dipendenti, Composites Aragón rende disponibili ai suoi clienti più di 30 anni di esperienza nella costruzione di stampi, materie plastiche e lavorazioni meccaniche. Per questo motivo oggi è in grado di operare in settori molto esigenti come quello dell'Aerospace e dell'Automotive, tra gli altri.
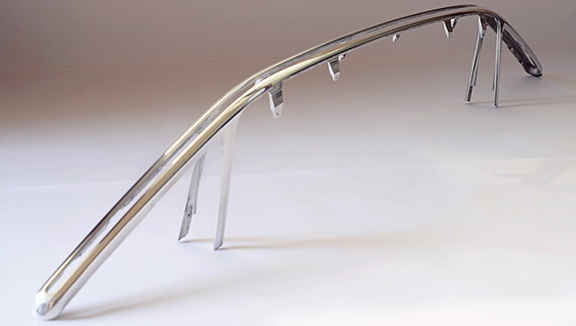
Il background di Composites Aragon
Il background di Composites Aragon nell’ingegneria applicata con CAD / CAM / CAE, combinato con la loro vasta esperienza nella progettazione di stampi e di processi produttivi, la loro competenza in molteplici tecnologie nella trasformazione delle materie plastiche così come le sinergie industriali che sono stati in grado di creare, ha permesso di sviluppare solide soluzioni attraverso le loro cinque divisioni di business:
- Lavorazione di compositi
- Fabbricazione di stampi
- Lavorazioni meccaniche
- Ingegnerizzazione
- Prototipazione
Questo mix di capacità e know-how ha portato Composites Aragon nel 2017 ad essere selezionata da Bugatti per la produzione/fornitura di un componente molto speciale della loro straordinaria nuova hypercar: la Bugatti Chiron. Oltre ad essere l'auto più veloce oggi disponibile sulle strade è un vero capolavoro di ingegneria automobilistica dove ogni singolo componente fa la differenza e perciò è stato studiato in ogni minimo dettaglio.
Il progetto tail light
Il componente di cui parliamo è lo speciale fanale posteriore della Chiron, che non solo dona a quest’auto un aspetto distintivo e unico ma è anche realizzato in conformità con le severe norme di illuminazione automobilistica. Un'unica superficie di emissione della luce, una linea a led incastonata in una cornice di lucido alluminio. Ogni singola cornice viene ricavata partendo da un unico blocco di Alluminio 6060 che pesa 197 kg e l'obiettivo non è solamente quello di avere il pezzo finito nel giusto tempo, ma di ottenere un elemento estremamente preciso nelle dimensioni e nella finitura lucida tendente all'effetto specchio. Non c'è spazio per imprecisioni, gradini o qualsiasi tipo di graffio.
Con la commessa della Chiron in fase di avvio, Composites Aragon si è resa conto che il parco macchine esistente non era probabilmente il più efficiente per questa applicazione. Fino al 2017, infatti, l'azienda spagnola nei propri stabilimenti si affidava sia a macchine indexabili con strutture rigide e pesanti ma troppo lente per una lavorazione competitiva dell'alluminio, sia a macchine a 5 assi con dinamica elevata ma troppo deboli per mantenere costanti precisioni e ripetibilità richieste da Bugatti.
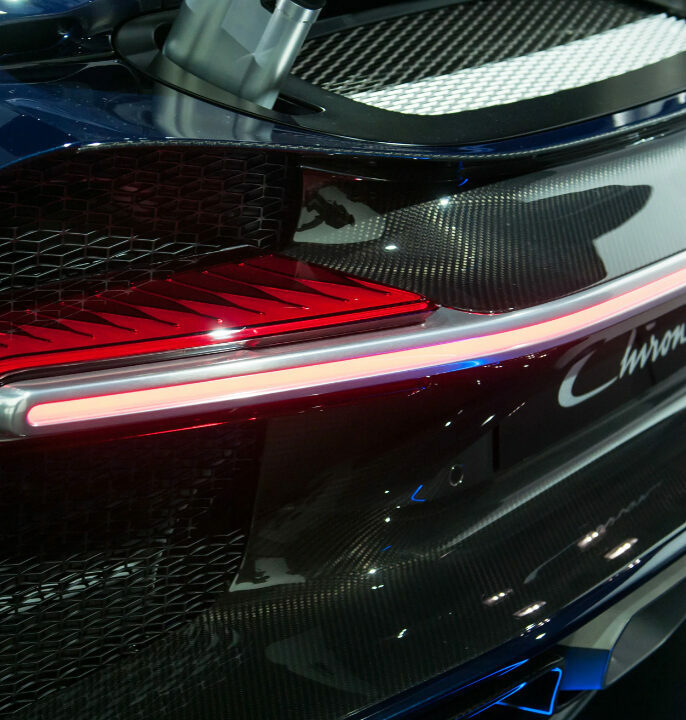
L'incontro con Breton
Claudio Monti (CEO di C.A.) e i suoi partner si sono messi così alla ricerca di una nuova soluzione in grado di coniugare rigidità e rapidità di movimento, precisione e velocità. L’azienda era sì pronta ad investire, ma solo per una macchina in grado di assicurare un rapido ritorno d'investimento.
Lavorando assieme a Breton alla definizione della soluzione più adatta, sia dal punto di vista delle performance che dei costi, Composites Aragon ha avuto la possibilità di valutare le prestazioni offerte dalla Raptor 1200. Con il giusto mix tra robustezza e dinamica e con i vantaggi della testa a forcella simmetrica, Raptor 1200 si è confermata la piattaforma ideale per il progetto "Chiron’s Tail Light".
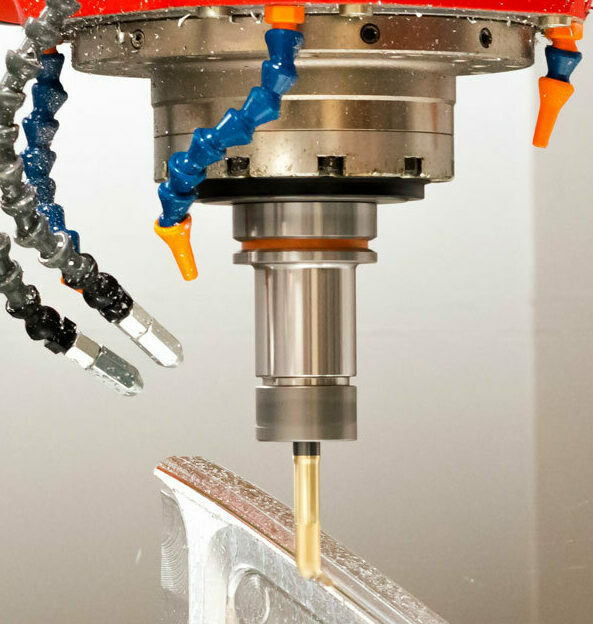
Breton Raptor 1200, la scelta giusta
La maggior parte delle macchine di classe simile sono progettate con travi che si muovono da sinistra a destra su ingombranti sostegni statici montati al di sopra delle porte d'accesso, rendendo così il caricamento del pezzo estremamente scomodo. Diversamente, l'architettura a portale alto della Raptor (con la trave gantry che si muove al di sopra di due colonne laterali e le ampie porte frontali) garantisce la più totale accessibilità per un carico/scarico dei pezzi rapido e sicuro, sia per mezzo di carroponti che di carrelli elevatori. La tavola è installata direttamente a terra a vantaggio dell'ergonomia e dell'evacuazione dei trucioli.
Tutto è progettato per rendere più facile e veloce l'attrezzaggio e il setup del pezzo. Non c'è bisogno di perdere tempo nell'allineare il pezzo, è sufficiente posizionare il materiale grezzo sull'attrezzatura, bloccarlo e lasciare che la macchina vada a tastare alcuni punti. Il ciclo di orientamento automatico del campo di lavoro fa il resto, orientando perfettamente e autonomamente la terna dei piani di lavoro e le origini del pezzo. Gli assi A e C sono dotati di potenti freni che possono bloccare rigidamente gli assi rotativi in qualsiasi posizione con precisione micrometrica, rendendo possibile anche la più piccola rototraslazione dei piani di lavoro.
L'approccio al Tail Light
Grazie alla rigidità della testa e alla sua geometria simmetrica, la cornice del Tail Light Chiron può essere bloccata verticalmente e raggiunta su 5 lati nello stesso staffaggio. Con una specifica strategia di fresatura multilivello dall'alto verso il basso, il pezzo viene sgrossato e finito senza essere rimosso dalle attrezzature ed evitando vibrazioni. Il supporto fornito da Breton a Composites Aragon è andato oltre l’individuazione della macchina corretta. È stato messo a disposizione del cliente il know-how per identificare strategie di fresatura ad alta efficienza e per scegliere gli utensili adatti, comprese specifiche spazzole di sbavatura e lucidatura non convenzionali. Anche le prestazioni del CNC sono state sfruttate al meglio per raggiungere la finitura lucida richiesta da Bugatti. Ciò ha incluso un'accurata messa a punto dei "compressori" spline e delle funzioni "Advanced Surface" disponibili sulla piattaforma Siemens Sinumerik. In sole 29,5 ore di ciclo completamente automatizzato, il blocco da 197 kg viene trasformato nella cornice Tail Light con dimensioni 1.629x241x67 mm e 1,5 kg di peso, accuratamente sagomata e lucida, pronta per essere montato sulla Chiron.
Dove sono i 197 kg di alluminio?
L'altezza dei montanti laterali e delle carenature della Raptor sono essenziali per contenere i trucioli ed evitare la proiezione verso il pavimento esterno dell'officina. Per quanto riguarda l’interno macchina, non si può far perdere tempo prezioso agli operatori lasciandogli il compito di spazzare e raccogliere tutti i trucioli dall'area di lavoro.
Nello studio del progetto, Raptor è stata adattata per interfacciarsi con il trasportatore trucioli centralizzato già esistente presso Composites Aragon e, aggiungendo uno speciale utensile-turbina per la rimozione dei trucioli con un ciclo automatico, si possono spingere tutti i residui di taglio sui nastri.
Raptor 1200 significa meno manodopera, tempi di lavorazione più brevi, maggiore precisione, elevata qualità della superficie e costi operativi ridotti.