
- Homepage
- Customer Stories
- Composites Aragon, das Tail Light des Bugatti Chiron
Customer story
Composites Aragon, das Tail Light des Bugatti Chiron
Wie stellt man den Rahmen für die Rückleuchte am Bugatti Chiron aus einem 197 kg schweren Aluminiumblock her und erhält zum Schluss ein komplett fertiges, poliertes Stück, das nur 1,5 kg wiegt?
Wenn man an Orte denkt, an denen Bauteile für die schnellsten Autos der Welt hergestellt werden, kommt einem vermutlich nicht gleich Spanien in den Sinn. Und doch stellt mitten in der Region Aragón, in Zaragoza, ein Unternehmen mit einer auf Flexibilität, Dynamik und das Erreichen anspruchsvoller Ziele ausgerichteten DNA Bauteile her, die in ihrer Art einzigartig sind.
Das Ende 2009 gegründete Unternehmen ist auf die Produktion von Bauteilen aus Verbundwerkstoffen spezialisiert und seine Stärke liegt im Management der gesamten Wertschöpfungskette: von der Konzeption über die Planung bis hin zur Entwicklung des fertigen Produkts. Durch die Bündelung der Kompetenzen von Management und Mitarbeitern stellt Composites Aragón seinen Kunden mehr als 30 Jahre Erfahrung in Formenbau, Kunststoffen und spanender Bearbeitung zur Verfügung. Aus diesem Grund kann das Unternehmen heute sehr anspruchsvolle Branchen wie beispielsweise Automobilindustrie und Luft- und Raumfahrt zu seinen Tätigkeitsfeldern zählen.
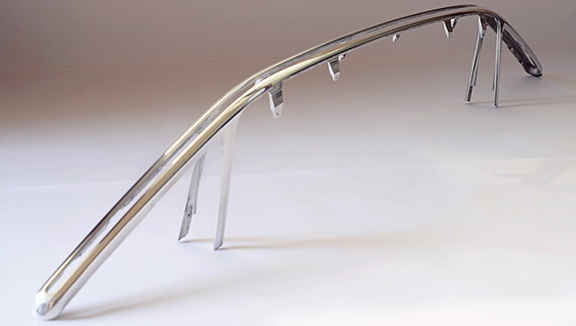
Der Background von Composites Aragon
Der Background von Composites Aragon in der angewandten Technik mit CAD/CAM/CAE in Kombination mit der umfassenden Erfahrung in der Gestaltung von Formen und Produktionsprozessen, dem Fachwissen über verschiedene Technologien in der Kunststoffverarbeitung sowie den geschaffenen industriellen Synergien ermöglichten dem Unternehmen die Entwicklung solider Lösungen über seine fünf Geschäftsbereiche:
- Zerspanung von Verbundwerkstoffen
- Formenbau
- Spanende Bearbeitung
- Engineering
- Prototyping
Diese Mischung aus Fähigkeit und Know-how führte dazu, dass Composites Aragon 2017 von Bugatti für die Produktion/Lieferung eines ganz besonderen Bauteils am außergewöhnlichen neuen Hypercar des Automobilherstellers ausgewählt wurde: dem Bugatti Chiron. Dieses Auto ist nicht nur das derzeit schnellste auf der Straße, sondern auch ein wahres Meisterwerk der Automobiltechnik, bei dem jede einzelne Komponente eine ganz entscheidende Rolle spielt und deshalb bis ins kleinste Detail durchdacht wurde.
Das Projekt Tail Light
Das Bauteil, von dem wir sprechen, ist die spezielle Rückleuchte des Chiron, die diesem Auto nicht nur ein unverwechselbares und einzigartiges Aussehen verleiht, sondern auch nach den strengen Normen für Fahrzeugbeleuchtung gefertigt wird. Eine einzige leuchtende Fläche, ein in einen Rahmen aus poliertem Aluminium eingefasstes LED-Lichtband.
Jeder einzelne Rahmen wird aus einem vollen Block aus 6060er Aluminium mit einem Gewicht von 197 kg gefräst. Dabei geht es nicht nur darum, das fertige Stück innerhalb der Zeitvorgabe herzustellen, sondern auch ein extrem maßhaltiges und beinahe spiegelartig poliertes Element zu fertigen. Für Ungenauigkeiten, Stufen oder irgendwelche Kratzer bleibt da kein Platz.
Als sich der Chiron-Auftrag in der Anlaufphase befand, erkannte Composites Aragon, dass der vorhandene Maschinenpark für diese Anwendung wohl nicht gerade effizient war. Bis 2017 setzte das spanische Unternehmen nämlich in seinen Werken entweder auf indexierbare Maschinen mit starrem, schwerem Aufbau, die aber für eine wettbewerbsfähige Aluminiumbearbeitung zu langsam waren, oder auf 5-Achsen-Maschinen mit hoher Dynamik, die aber zu schwach waren, um die von Bugatti geforderte konstante Präzision und Wiederholgenauigkeit zu gewährleisten.
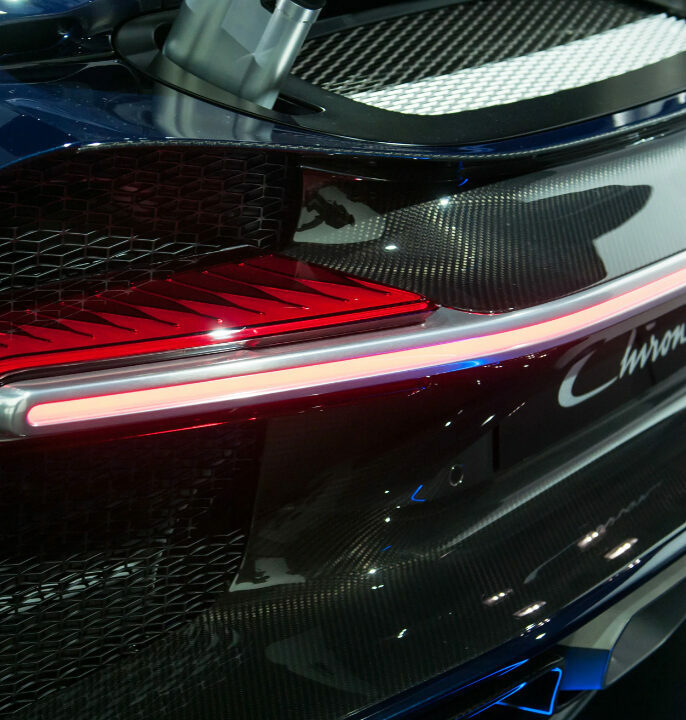
Das Zusammentreffen mit Breton
Claudio Monti (CEO von Composites Aragon) und seine Partner machten sich also auf die Suche nach einer neuen Lösung, die Steifigkeit und Bewegungsschnelligkeit, Präzision und Geschwindigkeit vereinen sollte. Das Unternehmen war durchaus bereit zu investieren, aber nur in eine Maschine mit gesicherter schneller Investitionsrentabilität.
Gemeinsam mit Breton arbeitete Composites Aragon an der Bestimmung der in Bezug auf Leistung und Kosten bestgeeigneten Lösung und hatte dabei auch Gelegenheit, die Leistung der Raptor 1200 zu beurteilen. Mit ihrer optimalen Mischung aus Robustheit und Dynamik und den Vorteilen des symmetrischen Gabelkopfs erwies sich die Raptor 1200 als ideale Plattform für das Projekt „Chiron’s Tail Light“.
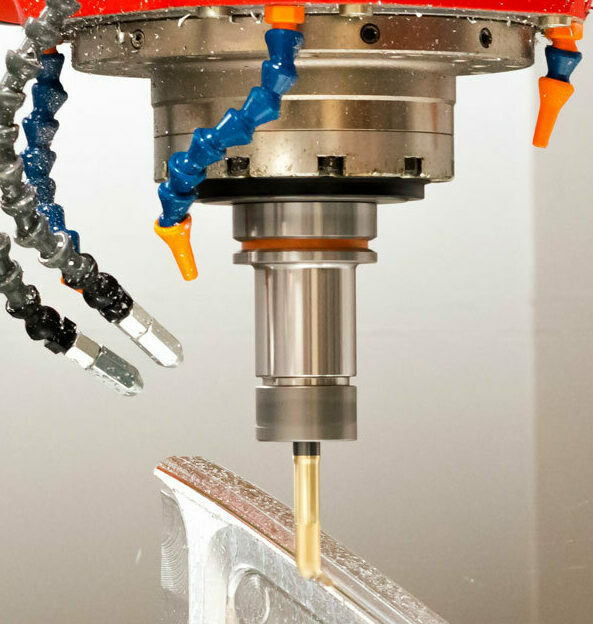
Breton Raptor 1200, die richtige Entscheidung
Die meisten Maschinen vergleichbarer Klasse sind mit Trägern konstruiert, die sich auf sperrigen statischen Stützen über den Zugangstüren von links nach rechts bewegen, was das Beladen mit Werkstücken extrem umständlich macht. Im Gegensatz dazu gewährleistet die Hochgantry-Bauweise der Raptor (mit einem über zwei Seitenständern verfahrenden Gantry-Träger und breiten Fronttüren) einen uneingeschränkten Zugang zum schnellen und sicheren Be- und Entladen von Werkstücken, wozu sowohl Laufkräne als auch Gabelstapler eingesetzt werden können. Der Maschinentisch ist direkt am Boden verankert, was sich vorteilhaft auf Ergonomie und Spanabtransport auswirkt.
Die gesamte Konstruktion zielt auf eine einfachere und schnellere Einrichtung von Werkzeugen und Werkstücken ab. Der Zeitaufwand für die Werkstückausrichtung entfällt komplett. Der Rohling wird einfach auf die Vorrichtung gelegt und eingespannt, woraufhin die Maschine ein paar Punkte antastet. Den Rest erledigt der automatische Ausrichtungszyklus des Arbeitsbereichs, der die drei Arbeitsebenen und die Werkstücknullpunkte perfekt und unabhängig voneinander ausrichtet. Die A- und C-Achsen sind mit leistungsstarken Bremsen ausgestattet, die die Drehachsen in jeder Position µm-genau fest arretieren können, so dass selbst kleinste Drehverschiebungen der Arbeitstische möglich sind.
Der beim Tail Light gewählte Ansatz
Dank der Steifigkeit des Kopfes und seiner symmetrischen Geometrie kann der Rahmen des Tail Light Chiron vertikal eingespannt und in der gleichen Einspannung von fünf Seiten erreicht werden. Mit einer speziellen mehrstufigen Frässtrategie von oben nach unten wird das Werkstück geschruppt und geschlichtet, ohne aus der Vorrichtung genommen zu werden. Gleichzeitig werden Vibrationen vermieden.
Der Support, mit dem Breton Composites Aragon zu Seite stand, ging über die Auswahl der richtigen Maschine hinaus. Dem Kunden wurde Know-how zur Erarbeitung hocheffizienter Frässtrategien und zur Auswahl geeigneter Werkzeuge, darunter spezielle, eher unübliche Entgratungs- und Polierbürsten, zur Verfügung gestellt.
Auch die CNC-Leistung wurde voll ausgenutzt, um die von Bugatti geforderte Polierung zu erreichen. Dies schloss die Feinabstimmung der Spline-„Kompressoren“ und der „Advanced Surface“-Funktionen ein, die auf der Plattform Sinumerik von Siemens zur Verfügung stehen. In nur 29,5 Stunden wird der 197 kg schwere Block in einem vollautomatischen Zyklus in den 1 629 x 241 x 67 mm großen und 1,5 kg schweren, präzise geformten und hochglänzenden Tail-Light-Rahmen verwandelt, der dann nur noch am Chiron eingebaut werden muss.
Wo sind die 197 kg Aluminium?
Die Höhe der Seitenständer und Verkleidungen an der Raptor dient dazu, Späne zurückzuhalten und zu verhindern, dass sie außerhalb der Arbeitsumgebung auf den Boden fallen. Was das Maschineninnere betrifft, dürfen die Maschinenbediener keine wertvolle Zeit mit dem Auffegen und Entfernen von Spänen aus dem Arbeitsbereich verschwenden.
In der Planungsphase wurde die Raptor so angepasst, dass sie mit dem bestehenden zentralen Späneförderer bei Composites Aragon verbunden werden konnte. Durch Hinzufügen einer speziellen Werkzeugturbine für die Späneabfuhr mit automatischem Zyklus können dann sämtliche Schneidrückstände auf Bänder befördert werden.
Die Raptor 1200 bedeutet weniger Arbeitskräfte, kürzere Bearbeitungszeiten, höhere Präzision, hohe Oberflächenqualität und geringere Betriebskosten.