
- Page d'accueil
- Customer Stories
- Composites Aragon, le feu arrière de la Bugatti Chiron
Customer story
Composites Aragon, le feu arrière de la Bugatti Chiron
Comment obtenir le cadre du feu arrière de la Bugatti Chiron à partir de 197 kg d’aluminium pour arriver à une pièce finie pesant seulement 1,5 kg ?
Lorsque que l’on pense aux endroits où sont produits les composants destinés aux voitures les plus rapides du monde, on ne pense pas immédiatement à l’Espagne. Et pourtant, c’est au cœur même de l’Aragon, à Saragosse, qu’une société totalement animée par la flexibilité, le dynamisme et la volonté d’atteindre des objectifs ambitieux, fabrique des composants uniques en leur genre.
Née à la fin de l’année 2009, cette société est spécialisée dans la production de matériaux composites, et sa force réside dans la gestion de l’intégralité de la chaine de valeur : du projet à la conception, jusqu’à la mise au point du produit fini. Unissant les compétences de ses managers et de ses employés, Composites Aragón met à disposition de se clients plus de 30 ans d’expérience en matière de fabrication de moules, de matières plastiques et d’usinage mécanique. C’est pourquoi aujourd’hui elle est en mesure d’évoluer dans des secteurs exigeants tels que l’aérospatiale et l’automobile, entre autres.
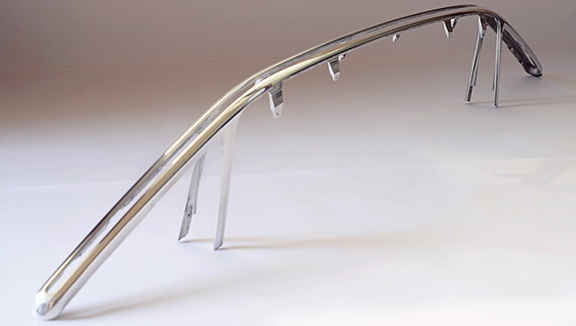
L’histoire de Composites Aragon
L’histoire de Composites Aragon dans le domaine de l’ingénierie appliquée avec CAO / FAO / IAO, associée à sa longue expérience dans la conception de moules et de processus de production, ses compétences concernant de nombreuses technologies de transformation des matières plastiques et les synergies industrielles qu’elle est parvenue à créer, ont permis de mettre au point des solutions solides au sein de ses cinq départements d’activité :
- Usinage de matériaux composites
- Fabrication de moules
- Usinage mécanique
- Ingénieurisation
- Prototypage
En 2017, cet ensemble de capacités et de savoir-faire a conduit Composites Aragon à être sélectionnée par Bugatti pour la production / finition d’un composant très spécial de sa nouvelle « hyper-voiture » : la Bugatti Chiron.
Non contente d’être la voiture la plus rapide disponible sur le marché, il s’agit d’un véritable chef d’œuvre d’ingénierie automobile, dont chaque composant est étudié dans le moindre détail afin de faire la différence.
Le projet feu arrière
Le composant qui nous intéresse est le feu arrière propre au modèle Chiron qui, en plus de conférer un aspect distinctif à cette voiture, a été réalisé conformément à des normes sévères d’éclairage automobile. Une surface d’émission lumineuse unique, une ligne à DEL enchâssée dans un entourage en aluminium brillant. Chaque entourage est fabriqué à partir d’un bloc unique d’aluminium 6060 de 197 kg, l’objectif n’étant pas uniquement de disposer de la pièce en temps voulu mais aussi d’obtenir un élément aux dimensions extrêmement précises, avec une finition brillante à l’aspect miroitant. Aucune place n’est laissée aux imprécisions, aux irrégularités ni aux rayures d’aucune sorte.
Lors de la phase de lancement de la commande du modèle Chiron, Composites Aragon s’est rendu compte que le parc automobile existant n’était probablement pas le plus efficace pour une telle application. En effet, jusqu’à 2017 la société espagnole disposait dans ses locaux de machines indexables aux structures lourdes et rigides mais trop lentes pour un usinage compétitif de l’aluminium, ainsi que de machines à 5 axes, hautement dynamiques mais trop peu résistantes pour satisfaire la précision et la répétabilité requises par Bugatti.
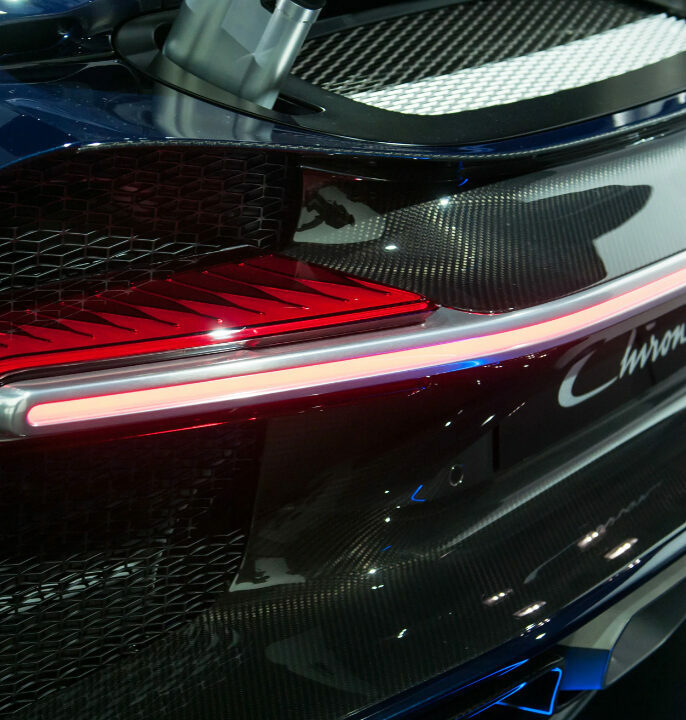
La rencontre avec Breton
Claudio Monti (PDG de Composites Aragon) et ses partenaires se sont donc mis à la recherche d’une nouvelle solution en mesure d’allier rigidité et rapidité de mouvement, précision et vitesse. La société était prête à investir, mais seulement pour une machine en mesure de garantir un retour sur investissement rapide.
En collaborant avec Breton à l’élaboration de la solution la plus adaptée, tant du point de vue des performances que des coûts, Composites Aragon a eu la possibilité d’évaluer les prestations proposées par le Raptor 1200. Avec le bon rapport entre robustesse et dynamique et les avantages de la tête à fourche symétrique, Raptor 1200 s’est imposée comme la plateforme idéale pour le projet « Chiron’s Tail Light ».
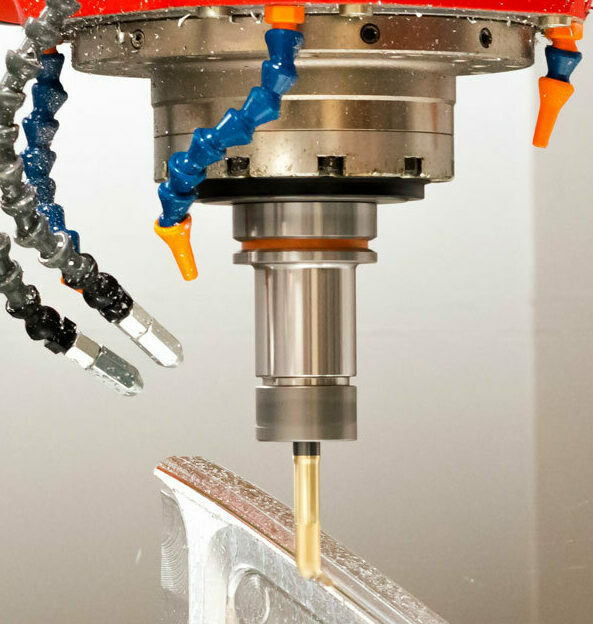
Raptor 1200 de Breton, le choix approprié
La plupart des machines de classe similaire ont été conçues avec des traverses se déplaçant de gauche à droite sur des supports statiques encombrants, montés au-dessus des portes de service, d’où un chargement des pièces particulièrement peu commode. En revanche, l’architecture à portique haut du modèle Raptor (avec une traverse de portique se déplaçant au-dessus de deux colonnes latérales et de grandes portes frontales) garantit l’accès le plus total pour un chargement / déchargement des pièces rapide et sûr, tant au moyen de ponts roulants que de chariots élévateurs.
La table est installée directement au sol, afin d’optimiser l’ergonomie et l’évacuation des copeaux.
Tout est conçu pour rendre l’ajustement et l’installation de la pièce plus faciles et rapides. Il n’est pas nécessaire de perdre du temps à aligner la pièce car il suffit de placer le matériau brut sur l’équipement et de laisser la machine tester certains points. Le cycle d’orientation automatique du champ de travail s’occupe du reste, en orientant parfaitement et de façon autonome les trois plans de travail et les points de référence de la pièce. Les axes A et C sont dotés de freins puissants en mesure de bloquer solidement les axes rotatifs dans n’importe quelle position avec une précision micrométrique, ce qui permet même les déplacements rotatifs les plus infimes des plans de travail.
L’approche feu arrière
Grâce à la rigidité de la tête et à sa géométrie symétrique, le cadre du modèle feu arrière Chiron peut être bloqué verticalement et rejoint sur 5 cotés pour un même serrage. Avec une stratégie spécifique de fraisage multi-niveaux du haut vers le bas, la pièce est dégrossie puis finie sans être retirée des équipements, et en évitant les vibrations. L’assistance fourni par Breton à Composites Aragon ne s’est pas limitée au fait de déterminer la machine appropriée. Il a été mis à disposition du client le savoir-faire nécessaire pour déterminer des stratégies de fraisage hautement efficaces et choisir les outils adaptés, notamment les brosses d’ébavurage et de polissage non conventionnelles. Les prestations de CNC ont également été utilisées au mieux pour obtenir la finition brillante exigée par Bugatti. Ceci inclut notamment une mise au point des « compresseurs » spline et des fonctions « Advanced Surface » disponibles sur la plateforme Siemens Sinumerik. En seulement 29,5 heures de cycle entièrement automatisé, le bloc de 197 kg est transformé en un cadre feu arrière de 1 629 x 241 x 67 mm et de 1,5 kg, façonné avec précision, brillant et prête à être monté sur la Chiron.
Où sont les 197 kg d’aluminium ?
La hauteur des montants latéraux et du carénage du Raptor sont essentiels pour contenir les copeaux et éviter leur projection sur le sol extérieur de l’atelier. S’agissant de l’intérieur de la machine, il convient d’éviter aux opérateurs de perdre un temps précieux à balayer et ramasser tous les copeaux de la zone de travail.
Lors de l’étude du projet, le Raptor a permis une interface avec le convoyeur à copeaux centralisé déjà présent chez Composites Aragon, avec l’ajout d’un outil-turbine spécial destiné au retrait des copeaux selon un cycle automatique qui permet de pousser tous les résidus de coupe vers les transporteurs.
Le Raptor 1200 est synonyme d’une moindre main d'œuvre, de temps d'usinage plus courts, d’une plus grande précision, d’une qualité de surface élevée et de coûts opérationnels réduits.