
- Pagina inicial
- Customer Stories
- Composites Aragon, o farol traseiro do Bugatti Chiron
Customer story
Composites Aragon, o farol traseiro do Bugatti Chiron
Como se obtém a moldura do farol traseiro do Bugatti Chiron, partindo de 197 kg de alumínio e chegando à peça completamente acabada e polida de apenas 1,5 kg de peso.
Quando se pensa nos locais em que são produzidos os componentes para os automóveis mais velozes do mundo não é Espanha que nos vem imediatamente à cabeça. Contudo, exatamente no coração da região de Aragão, em Saragoça, uma empresa com um ADN consagrado à flexibilidade, ao dinamismo e à satisfação de objetivos desafiantes está a fabricar componentes únicos do seu género.
Surgida nos finais de 2009, a empresa especializou-se na produção de componentes em material compósito. A sua grande mais-valia está na gestão de toda a cadeia de valor: desde a idealização, passando pela conceção, até ao ajuste do produto acabado. Ao unir as competências da gestão e dos funcionários, a Composites Aragón coloca ao dispor dos seus clientes mais de 30 anos de experiência na produção de moldes, materiais de plástico e maquinações. Por este motivo, hoje em dia é capaz de operar em setores muito exigentes, como o aeroespacial e automóvel, entre outros.
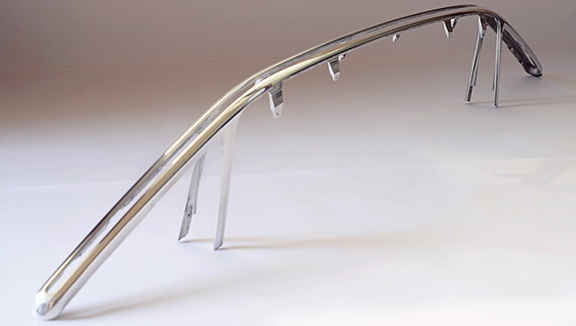
O passado da Composites Aragon
O passado da Composites Aragon em engenharia aplicada com CAD/CAM/CAE, aliado à sua vasta experiência na conceção de moldes e de processo de produção, e à sua competência em inúmeras tecnologias de transformação de materiais plásticos, assim como as sinergias industriais que conseguiram criar, permitiu desenvolver soluções sólidas nas cinco divisões de negócio:
- Composite machining
- Fabrico de moldes
- Maquinações
- Engenharia
- Prototipagem
Este conjunto de capacidades e de conhecimentos técnicos fez com que a Composites Aragon tenha sido selecionada, em 2017, pela Bugatti para produzir e fornecer um componente muito especial do seu novo e extraordinário supercarro: o Bugatti Chiron.
Além de ser o automóvel mais veloz em estrada atualmente disponível, é uma verdadeira obra-prima de engenharia automóvel, onde cada componente faz a diferença e, por isso, foi estudado ao mínimo detalhe.
O projeto do farol traseiro
O componente de que falamos é o farol traseiro especial da Chiron, que não só dá um visual distinto e único a este carro, como também foi produzido em conformidade com as rígidas normas de iluminação para automóveis. Uma única superfície de emissão de luz, uma fila de LED engastada numa moldura de alumínio polido. Cada uma das molduras surge de um único bloco de alumínio 6060, que pesa 197 kg. O objetivo não é apenas ter uma peça acabada no tempo definido, mas antes obter um elemento extremamente preciso em termos de dimensões e de acabamento do polimento que pretende obter um efeito espelhado. Não há espaço para imprecisões, gradações ou qualquer tipo de riscos.
Quando começou a encomenda do Chiron, a Composites Aragon apercebeu-se de que o parque de máquinas existente não era, provavelmente, o mais eficiente para esta aplicação. Na verdade, até 2017, a empresa espanhola recorria tanto a máquinas indexadoras com estruturas rígidas e pesadas, mas demasiado lentas para uma maquinação competitiva do alumínio, como também a máquinas de 5 eixos com uma dinâmica elevada, mas demasiado fracas para manter a precisão e a repetibilidade exigidas pela Bugatti.
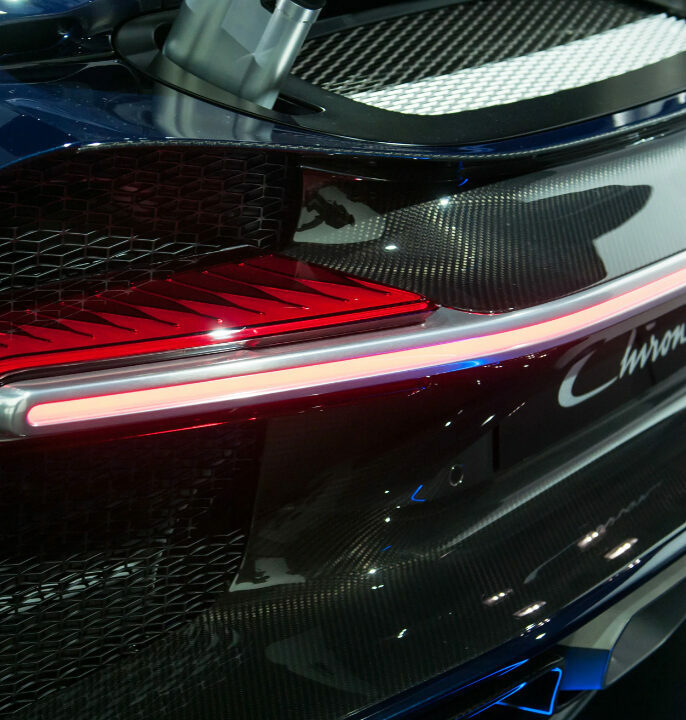
Reunião com a Breton
Claudio Monti (CEO da Composites Aragon) e os seus parceiros começaram a procurar uma nova solução capaz de unir rigidez e rapidez de movimentação, precisão e velocidade. A empresa estava pronta para investir, mas apenas numa máquina que pudesse garantir um retorno rápido do investimento.
Em parceria com a Breton, a Composites Aragon empenhou-se no desenvolvimento da solução mais adequada, tanto do ponto de vista do desempenho, como dos custos, e conseguiu gerar valor a partir das prestações da Raptor 1200. Com o nível certo de robustez e dinamismo e com a vantagem de possuir uma cabeça de garfo simétrico, a Raptor 1200 deu provas de ser a plataforma ideal para o projeto «Chiron’s Tail Light» (farol traseiro do Chiron).
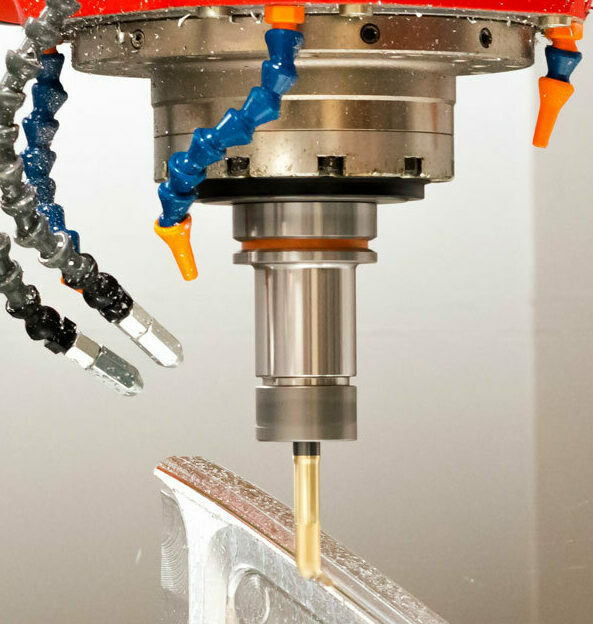
Breton Raptor 1200, a escolha certa
A maior partes das máquinas de classe semelhante foi projetada com traves que se deslocam da esquerda para a direita em apoios volumosos estáticos e montados sobre as portas de acesso, o que torna o carregamento da peça muito incómodo. Pelo contrário, a arquitetura de pórtico alto da Raptor (a trave do pórtico desloca-se sobre as duas colunas laterais e as amplas portas dianteiras) garante a maior acessibilidade possível para uma carga/descarga rápida e segura das peças, seja com a ponte rolante, seja com os carros elevadores. A mesa está instalada diretamente no solo, com a vantagem da ergonomia e da eliminação das limalhas.
Tudo foi projetado para garantir que equipar e configurar a peça é mais simples e rápido. Não é necessário perder tempo para alinhar a peça. Basta posicionar o material bruto no equipamento, bloqueá-lo e permitir que a máquina sonde alguns pontos. O ciclo de orientação automática do campo de trabalho trata do resto, ao orientar na perfeição e com autonomia os três planos de trabalho e as origens da peça. Os eixos A e C estão equipados com potentes travões que podem bloquear com rigidez os eixos rotativos em qualquer posição e com precisão micrométrica, tornando possível até mesmo a mais pequena translação rotativa das mesas de trabalho.
A aproximação ao farol traseiro
Graças à rigidez da cabeça e à sua geometria simétrica, a moldura do farol traseiro do Chiron pode ser bloqueada na vertical e alcançada a partir de 5 lados na mesma fixação. Com uma estratégia de fresagem multinível de alto a baixo, a peça é desbastada e acabada sem que os equipamentos tenham de ser removidos e evitando vibrações. O apoio dado pela Breton à Composites Aragon alargou-se muito para lá da definição da máquina correta. O cliente teve à sua disposição o conhecimento técnico necessário para identificar estratégias de fresagem de eficiência elevada e para escolher as ferramentas adaptadas, incluindo escovas de rebarbamento e polimento não convencionais. As prestações do CNC foram aproveitadas ao máximo para alcançar o acabamento polido solicitado pela Bugatti. Entre eles está o ajuste preciso dos «compressores» e das funções «Advanced Surface» disponíveis na plataforma Siemens Sinumerik. Em apenas 29,5 horas, o ciclo completamente automatizado transforma o bloco de 197 kg na moldura do farol traseiro, com um tamanho de 1629 x 241 x 67 mm e 1,5 kg de peso, cuidadosamente perfilada e polida, pronta para ser montada no Chiron.
Onde estão os 197 kg de alumínio?
A altura das colunas laterais e das carenagens da Raptor foram essenciais para conter as limalhas e evitar a projeção para o pavimento exterior da oficina. No que diz respeito ao interior da máquina, os operadores têm coisas mais importantes para fazer do que varrer e recolher as limalhas da área de trabalho.
Durante a avaliação do projeto, a Raptor foi adaptada para funcionar como interface para o extrator de limalhas centralizado já existente na Composites Aragon. Com uma ferramenta-turbina para a remoção das limalhas com um ciclo automático, é possível direcionar todos os resíduos de corte para as correias.
A Raptor 1200 significa menos mão-de-obra, tempos de maquinação mais curtos, mais precisão, qualidade elevada da superfície e custos operacionais reduzidos.