
- Homepage
- Customer Stories
- Composites Aragón, la luz de cola del Bugatti Chiron
Customer story
Composites Aragón, la luz de cola del Bugatti Chiron
¿Cómo se obtiene el marco de la luz posterior del Bugatti Chiron a partir de 197 kg de aluminio para llegar a una pieza completamente terminada y pulida de solo 1,5 kg di peso?
Cuando se piensa en los lugares donde se fabrican los productos y componentes para los automóviles más rápidos del mundo lo primero que viene a la mente no es España. Pero en el corazón de Aragón, en Zaragoza, una empresa con un ADN volcado en la flexibilidad, el dinamismo y la consecución de objetivos retadores está fabricando componentes únicos en su género.
Nacida a finales de 2009, la empresa se ha especializado en la producción de componentes de material compuesto y su punto fuerte se encuentra en la gestión de toda la cadena de valor: de la idea y el proyecto hasta llegar a la puesta a punto del producto terminado. Combinando las capacidades de dirección y empleados, Composites Aragón pone a disposición de sus clientes más de 30 años de experiencia en la construcción de moldes, materiales plásticos y elaboraciones mecánicas. Gracias a ello, actualmente puede operar en sectores muy exigentes como el aeroespacial o el automovilístico entre otros.
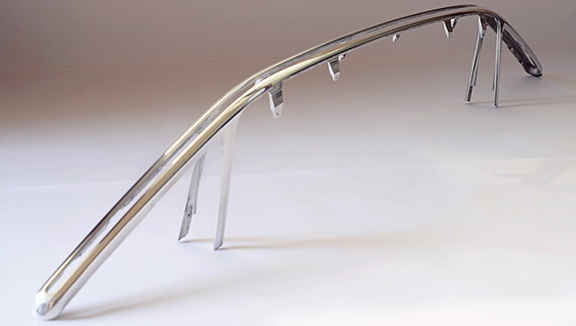
Los antecedentes de Composites Aragón
Los antecedentes de Composites Aragón en la ingeniería aplicada con CAD/CAM/CAE, combinados con su amplia experiencia en el proyecto de moldes y procesos productivos, su competencia en muchas tecnologías de la transformación de las materias plásticas, así como las sinergias industriales que han conseguido crear, han permitido desarrollar sólidas soluciones a través de sus cinco divisiones de negocio:
- Mecanizado de materiales compuestos
- Fabricación de moldes
- Elaboraciones mecánicas
- Ingeniería
- Prototipado
Esta mezcla de capacidad y conocimiento práctico ha llevado a Composites Aragón en 2017 a ser elegida por Bugatti para la fabricación/suministro de un componente muy especial de su extraordinario nuevo hipercoche: el Bugatti Chiron.
Además de ser el coche más rápido disponible actualmente en las carreteras, es una verdadera obra maestra de ingeniería automovilística en la que cada componente marca la diferencia y por eso se ha estudiado hasta el más mínimo detalle.
El proyecto luz de cola
El componente del que hablamos es la especial luz posterior del Chiron, que no solo da a este coche un aspecto distintivo y único si no que también está realizado de acuerdo con las estrictas normas de iluminación automovilística. Una única superficie de emisión de la luz, una línea led encastrada en un marco de aluminio pulido. Cada marco se mecaniza partiendo de un único bloque de aluminio 6060 que pesa 197 kg y el objetivo no es solo el de tener la pieza terminada justo a tiempo sino obtener un elemento extremadamente preciso en sus dimensiones y en el acabado pulido tendente al efecto espejo. No hay lugar para imprecisiones, resaltes ni cualquier tipo de arañazo.
Con el pedido del Chiron en fase de puesta en marcha, Composites Aragón se dio cuenta de que el parque de maquinaria existente no era probablemente el más eficiente para esta aplicación. Hasta 2017, de hecho, la empresa española confiaba en sus instalaciones bien a máquinas indexables de estructura rígida y pesada pero demasiado lentas para un mecanizado competitivo del aluminio, bien a máquinas de cinco ejes con dinámica elevada pero demasiado débiles para mantener constantes las precisiones y repetibilidad exigidas por Bugatti.
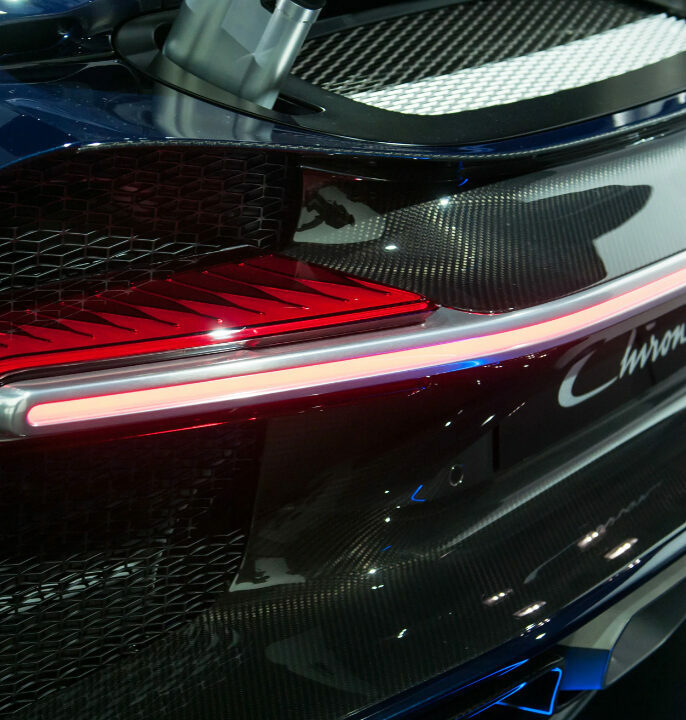
El encuentro con Breton
Claudio Monti (CEO de C.A.) y sus socios se pusieron pues a la búsqueda de una nueva solución capaz de conjuntar rigidez y rapidez de movimiento, precisión y velocidad. La empresa estaba dispuesta a invertir, pero solo por una máquina que garantizara un rápido retorno de la inversión.
Trabajando junto a Breton en la definición de la solución más adecuada desde el punto de vista tanto de las prestaciones como de los costes, Composites Aragón tuvo la posibilidad de evaluar las prestaciones ofrecidas por la Raptor 1200. Con la justa combinación entre robustez y dinámica y las ventajas de la cabeza de horquilla simétrica, Raptor 1200 se ha confirmado como la plataforma ideal para el proyecto «Chiron’s Tail Light» (luz de cola del Chiron).
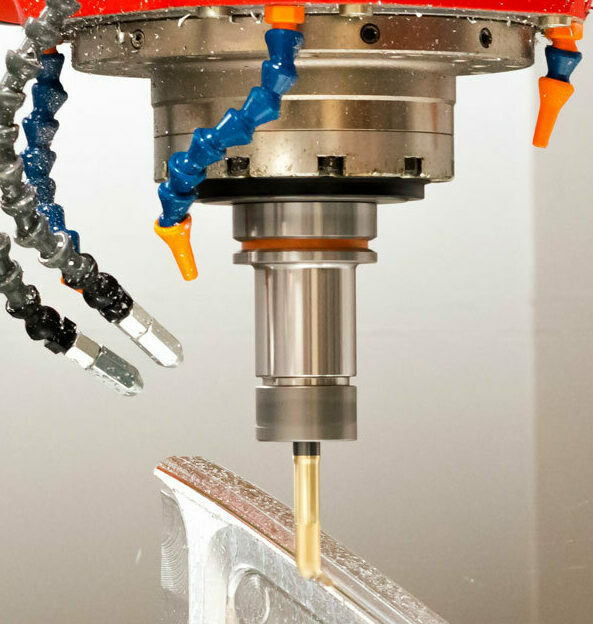
Breton Raptor 1200, la elección adecuada
La mayor parte de máquinas de clase similar se proyectan con travesaños que se mueven de izquierda a derecha sobre voluminosos soportes estáticos montados sobre la puerta de acceso, lo que hace extremadamente incómoda la carga de la pieza. En cambio, la arquitectura de pórtico de la Raptor (con el travesaño de pórtico que se desplaza sobre dos columnas laterales y las amplias puertas frontales) garantiza una accesibilidad total para la carga/descarga de piezas rápida y segura, tanto mediante puentes-grúa como carretilla elevadora. La mesa se instala directamente en el suelo, favoreciendo la ergonomía y la evacuación de las virutas.
Todo se ha proyectado para hacer más fáciles y rápidas la preparación y configuración de la pieza.
No es necesario perder el tiempo alineando la pieza, basta colocar el material en bruto sobre el equipamiento de sujeción, bloquearlo y dejar que la máquina palpe algunos puntos. El ciclo de orientación automática del campo de trabajo hace el resto, orientando perfecta y autónomamente la terna de las mesas de trabajo y los orígenes de la pieza. Los ejes A y C disponen de potentes frenos que pueden bloquear rígidamente los ejes giratorios en cualquier posición con precisión micrométrica, haciendo posible además la más pequeña rototraslación de las mesas de trabajo.
El enfoque de la luz de cola
Gracias a la rigidez de la cabeza y a su geometría simétrica, el marco de la luz de cola del Chiron puede bloquearse verticalmente y mecanizarse en cinco lados con el mismo amarre. Con una estrategia de fresado multinivel específica de arriba hacia abajo, la pieza se desbasta y acaba sin retirarla del equipamiento y evitando vibraciones. El apoyo proporcionado por Breton a Composites Aragón no se ha limitado a determinar la máquina correcta. Se puso a disposición del cliente el conocimiento práctico para identificar estrategias de fresado de alta eficiencia y para elegir las herramientas adecuadas, incluidos unos especiales cepillos de desbarbado y pulido no convencionales. También las prestaciones del CNC se han aprovechado al máximo para conseguir el acabado pulido exigido por Bugatti. Esto ha incluido una precisa puesta a punto de los «compresores» de spline y las funciones de superficie avanzada disponibles en la plataforma Siemens Sinumerik. En solo 29,5 horas de ciclo completamente automatizado, el bloque de 197 kg se convierte en el marco de la luz de cola, con unas dimensiones de 1629 x 241 x 67 mm y 1,5 kg de peso, perfilado y pulido con precisión para montarlo en el Chiron.
¿Donde están los 197 kg de aluminio?
La altura de los montantes laterales y los carenados de la Raptor son esenciales para contener las virutas y evitar la proyección hacia el suelo externo del taller. Por lo que respecta al interior de la máquina, no se puede hacer perder su valioso tiempo a los operadores dejándoles la tarea de barrer y recoger todas las virutas del área de trabajo.
En el estudio del proyecto, Raptor se adaptó para interconectarse con el transportador de virutas centralizado ya existente en Composites Aragón y, añadiendo una herramienta-turbina especial para la extracción de virutas con un ciclo automático, se pueden empujar todos los residuos de corte hacia las cintas.
Raptor 1200 significa menos mano de obra, menores tiempos de mecanizado, mayor precisión, elevada calidad de la superficie y costes operativos reducidos.