
- Homepage
- Customer Stories
- Composites Aragon, Bugatti chiron's tail light
Customer story
Composites Aragon, Bugatti chiron's tail light
How you get the Bugatti Chiron rear light frame from 197 kg of aluminium to the fully finished and polished part weighing just 1.5 kg
When you think of places where the fastest car parts in the world are produced, Spain does not immediately come to mind. On the contrary, in the very heart of the Aragon region, in Zaragoza, a company whose DNA is devoted to flexibility, dynamism and challenging goals is manufacturing unique components.
Established at the end of 2009, the company has been specialising in the production of composite components; its strength lies in the management of the entire value chain, from conception to design, right through to the finished product. By combining management and employee skills, Composites Aragón puts more than 30 years of experience in mould making, plastics and machining at its customers service. For this reason, it is nowadays able to operate in very demanding sectors such as Aerospace and Automotive, among others.
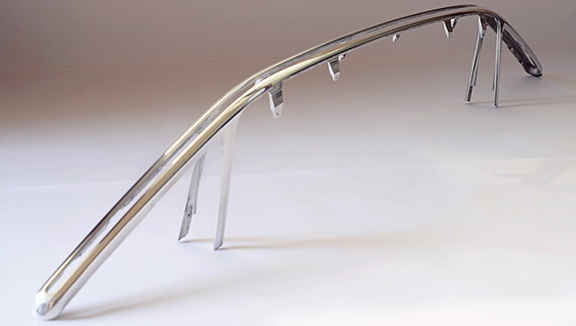
Composites Aragon's background
Composites Aragon's background in applied engineering with CAD / CAM / CAE combined with their extensive experience in mould and process design, their expertise in multiple technologies in plastics processing as well as the industrial synergies they have been able to create, has allowed them to develop solid solutions through their five business divisions:
- Composite machining
- Mould manufacturing
- Mechanical machining
- Engineering
- Prototyping
Composites Aragon's mix of skill and know-how made it get selected by Bugatti in 2017 for the production/supply of a very special component of their extraordinary new hypercar: the Bugatti Chiron.
Besides being the fastest car available on the roads today, it is a true masterpiece of automotive engineering where every single component makes the difference, since it has been studied in every detail.
The tail light project
The component we are talking about is the Chiron's special rear light, which not only gives this car a distinctive and unique look, but has also been manufactured in accordance with the strict automotive lighting standards. A single light-emitting surface, a LED line embedded in a polished aluminium frame. Each single frame is made from a single block of Aluminum 6060 that weighs 197 kg; the goal is not just to have the finished piece in the right time, but to obtain an extremely precise element in size with a glossy finishing aiming at a mirror effect. There is no room for inaccuracies, mismatches or any kind of scratch. With the Chiron order in the start-up phase, Composites Aragon realised that the existing fleet of machines was probably not the most efficient for this application. Until 2017, in fact, the Spanish company relied on both indexable machines with rigid and heavy structures but too slow for competitive aluminium machining, and 5-axis machines with high dynamics but too weak to maintain the constant accuracy and repeatability required by Bugatti.
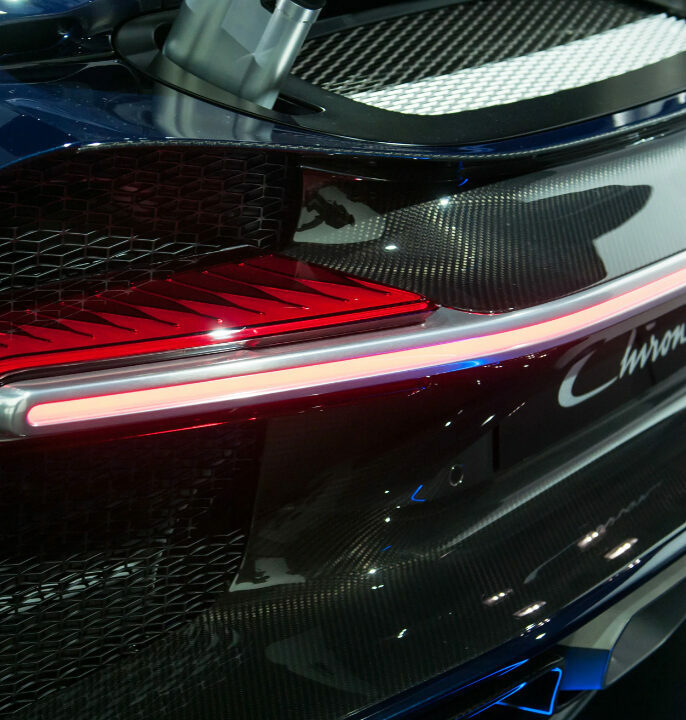
The meeting with Breton
Claudio Monti (CEO of C.A.) and his partners started looking for a new solution that combined rigidity and speed of movement, precision and rapidity. The company was ready to invest, but only for a machine capable of ensuring a rapid return on investment.
Working together with Breton to define the most suitable solution, both in terms of performance and cost, Composites Aragon had the opportunity to evaluate the performance offered by the Raptor 1200. With the right mix of robustness and dynamics and the advantages of the symmetrical fork head, Raptor 1200 proved to be the ideal platform for the "Chiron's Tail Light" project.
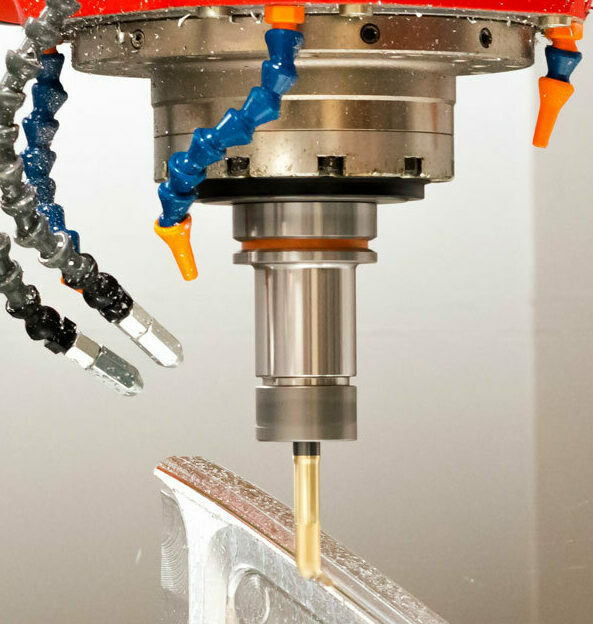
Breton Raptor 1200, the right choice
Most machines of similar class are designed with beams that move from left to right on bulky static supports mounted above the access doors, making the workpiece loading extremely uncomfortable. In comparison, the Raptor's high gantry architecture (with the gantry beam moving above two side columns and the large front doors) ensures total accessibility for fast and safe part loading/unloading, both by means of overhead cranes and forklifts. The table is installed directly on the ground for the benefit of ergonomics and chip evacuation.
Everything is designed to make tooling and part setup easier and faster. There is no need to waste time in aligning the workpiece, simply place the raw material on the fixture, clamp it and let the machine probe some points. The automatic work field orientation cycle does the rest, perfectly and independently orienting the work table trio and the workpiece origins.The A and C axes are equipped with powerful brakes that can rigidly lock the rotary axes in any position with micrometric precision, making even the smallest roto-traslation of the working tables possible.
The Tail Light approach
Thanks to its head rigidity and symmetrical geometry, the frame of the Tail Light Chiron can be locked vertically and reached on 5 sides in the same bracket. With a specific multi-level milling strategy from top to bottom, the workpiece is roughened and finished without being removed from the fixtures and avoiding vibrations. The support provided by Breton to Composites Aragon has gone beyond finding the correct machine. The know-how was made available to the customer to identify highly efficient milling strategies and to choose the right tools, including specific unconventional deburring and polishing brushes. The CNC performance was also used to achieve the polished finish required by Bugatti. This included careful fine-tuning of the spline "compressors" and "Advanced Surface" functions available on the Siemens Sinumerik platform. In just 29.5 hours of fully automated cycle time, the 197 kg block is transformed into an accurately shaped and polished Tail Light frame of 1,629x241x67 mm weighing 1.5 kg, ready to be mounted on the Chiron.
Where did 195.5 kg of aluminium go?
The height of the Raptor's side columns and fairings are essential to contain swarf and prevent it from projecting to the floor outside the workshop. With regard to the inside of the machine, you cannot waste valuable time leaving the operators to sweep and collect all the swarf from the work area.
In the study of the project, Raptor has been adapted to interface with the centralized chip conveyor already existing at Composites Aragon and, by adding a special tool-turbine for chip removal with an automatic cycle, all cutting residues can be pushed onto the belts.
Raptor 1200 means less manpower, shorter processing times, higher accuracy, higher surface quality and lower operating costs.